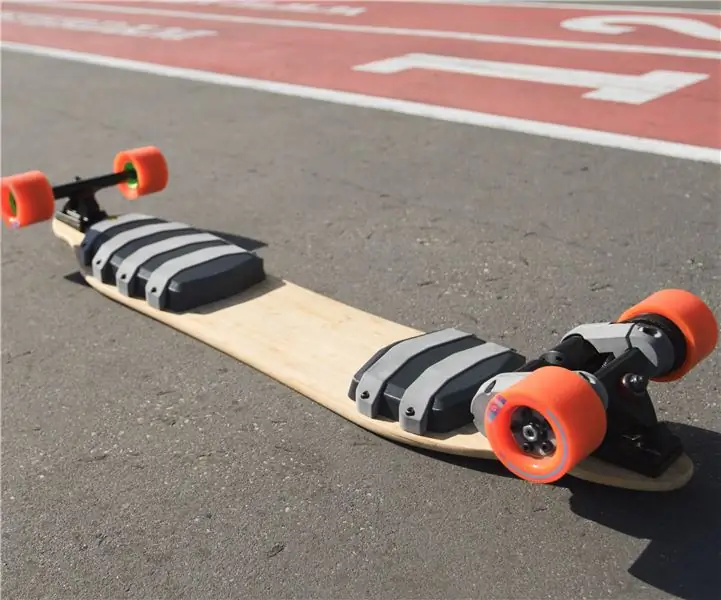
Taula de continguts:
2025 Autora: John Day | [email protected]. Última modificació: 2025-01-23 14:38
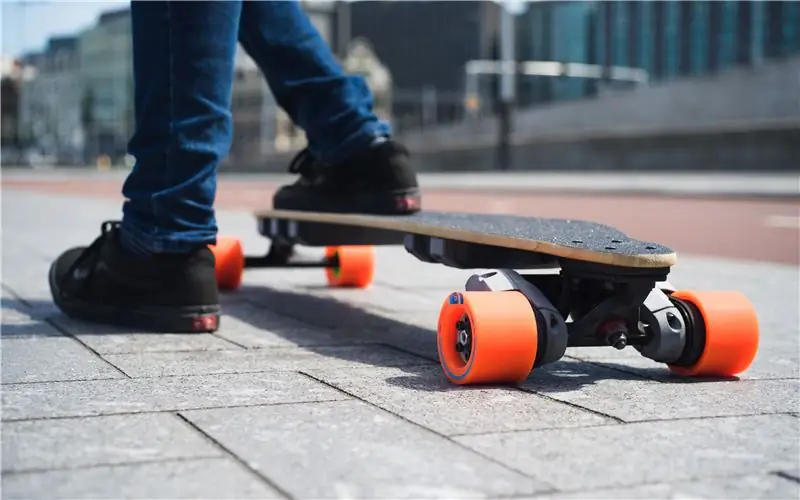
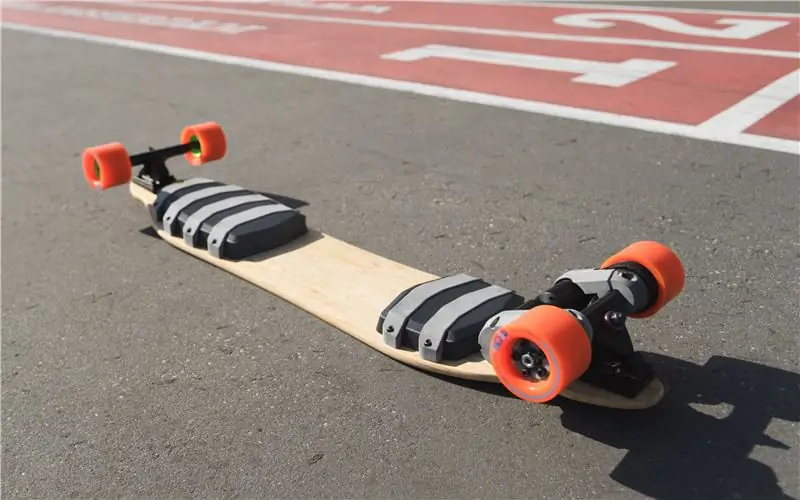
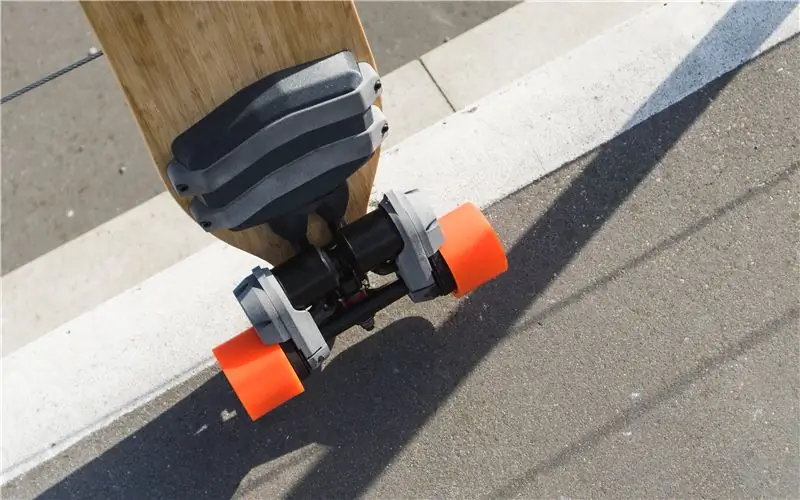
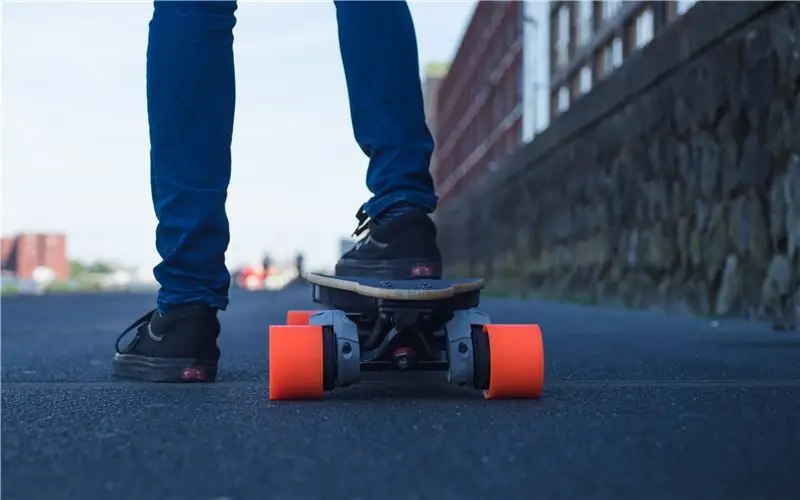
Aquest instructiu és una visió general del procés de compilació de la placa electrònica Fusion que vaig dissenyar i construir mentre treballava a 3D Hubs. El projecte va rebre l’encàrrec de promoure la nova tecnologia HP Multi-Jet Fusion que ofereixen els concentradors 3D i mostrar diverses tecnologies d’impressió 3D i com es poden combinar eficaçment.
Vaig dissenyar i construir un longboard motoritzat elèctric, que es pot utilitzar per a viatges curts a moderats o en combinació amb transport públic per oferir un abast de viatges molt més ampli. Té una velocitat màxima elevada, és molt maniobrable i es transporta fàcilment quan no s’utilitza.
Pas 1: procés de disseny
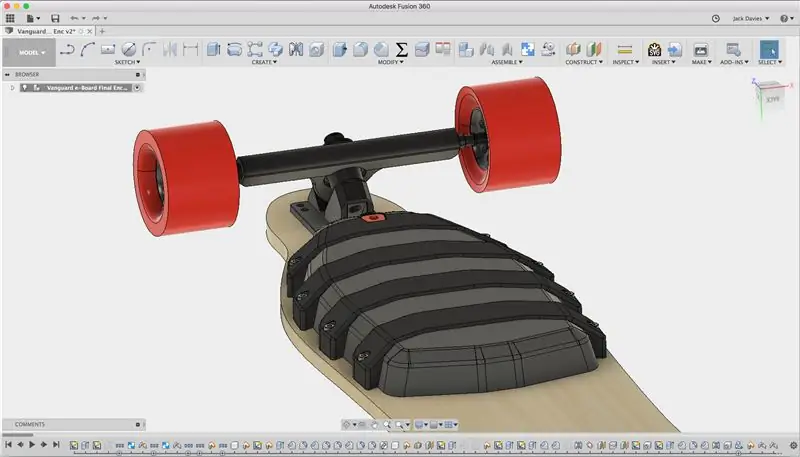
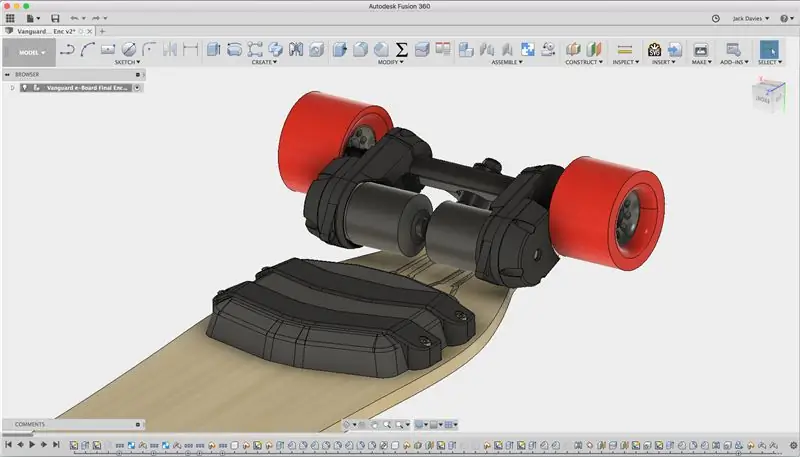
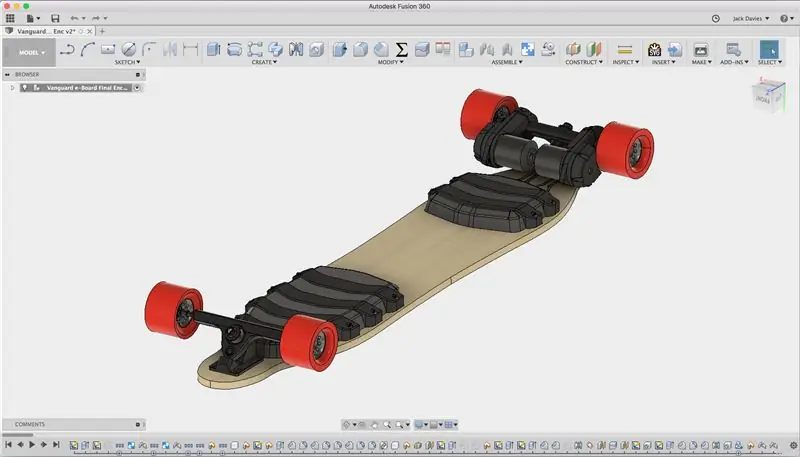
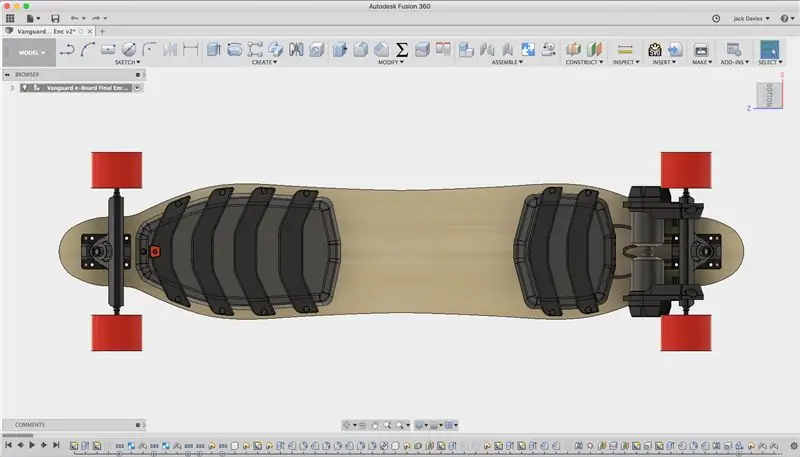
Vaig començar el projecte identificant els principals components estàndard del longboard; camions, coberta i rodes. Estaven fora de les prestatgeries, de manera que les vaig utilitzar com a punt de partida del disseny. La primera etapa va ser dissenyar la transmissió, que inclou els muntatges del motor, la configuració de l’engranatge i va incloure algunes modificacions als camions. La mida i la posició dels muntatges del motor determinarien la mida i la ubicació dels tancaments, de manera que era important que es completés primer. Vaig calcular els requisits de velocitat màxima i parell desitjats que em van permetre seleccionar els motors i la bateria de la placa. També es va calcular la relació d'engranatges i es van seleccionar les mides de les politges, juntament amb la longitud de la corretja motriu. Això em va permetre esbrinar la mida correcta dels muntatges del motor que asseguraven una corretja ben tensada.
La següent etapa va ser dissenyar els recintes del controlador de bateria i velocitat (ESC). La coberta seleccionada està formada principalment per bambú, de manera que és força flexible i es doblega substancialment al centre. Això té avantatges de ser còmode de conduir, ja que absorbeix els ressalts a la carretera i no els transfereix al pilot. Tanmateix, això també significa que es necessita un allotjament dividit per allotjar la bateria i l'electrònica, ja que un allotjament complet no es podria flexionar amb la placa i entraria en contacte amb el terra durant el funcionament. Els controladors electrònics de velocitat (ESC) es van col·locar més a prop dels motors a causa de restriccions elèctriques. Com que els motors s’uneixen a través dels camions, la posició canvia durant els girs, de manera que el recinte va haver de ser dissenyat per permetre la separació dels motors.
El sistema de bateries es col·locava a l’altre extrem de la coberta i allotjava l’electrònica relacionada amb la potència. Això incloïa el paquet de bateries, format per 20 cèl·lules de ions de liti 18650, el sistema de gestió de bateries, l’interruptor d’encesa / apagat i el sòcol de càrrega.
Vaig utilitzar Autodesk Fusion360 per a tot el procés de disseny, aquest programari em va permetre modelar ràpidament components dins del conjunt principal, cosa que va accelerar considerablement el temps de desenvolupament. També he utilitzat les funcions de simulació de Fusion360 per assegurar-me que les parts serien prou resistents, especialment els muntatges del motor. Això em va permetre reduir la mida de les muntures, ja que vaig poder verificar els requisits de resistència i deflexió i eliminar el material mantenint un factor de seguretat adequat. Un cop finalitzat el procés de disseny, va ser molt fàcil exportar les parts individuals per a la impressió 3D.
Pas 2: transmissió
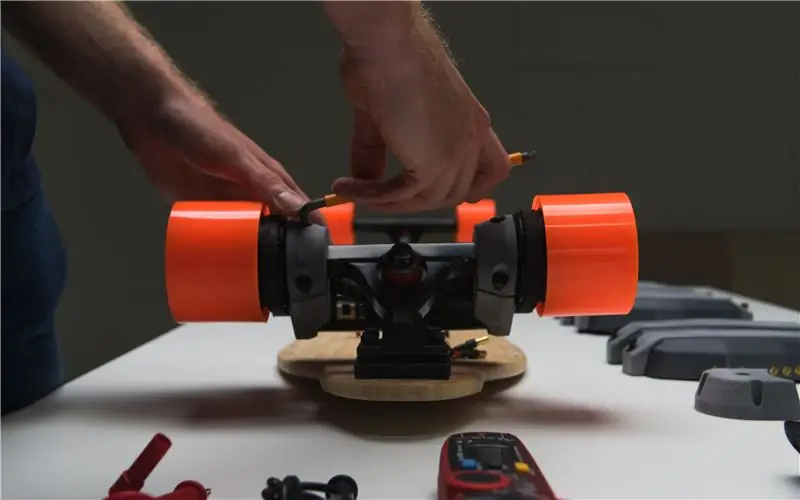
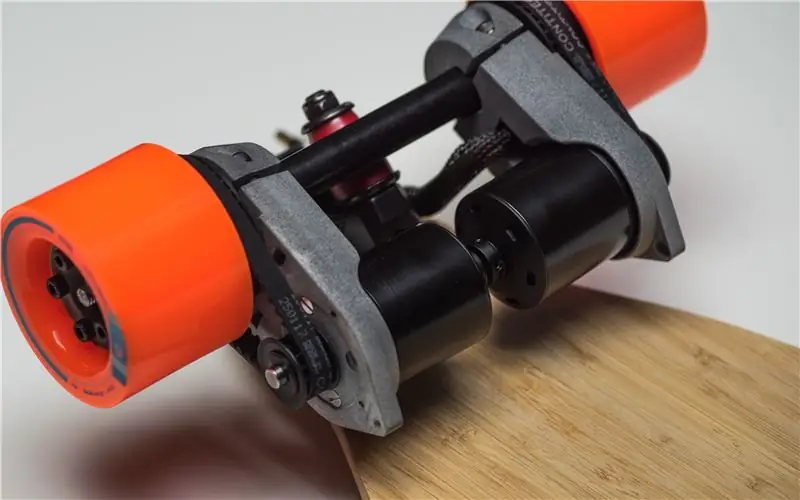
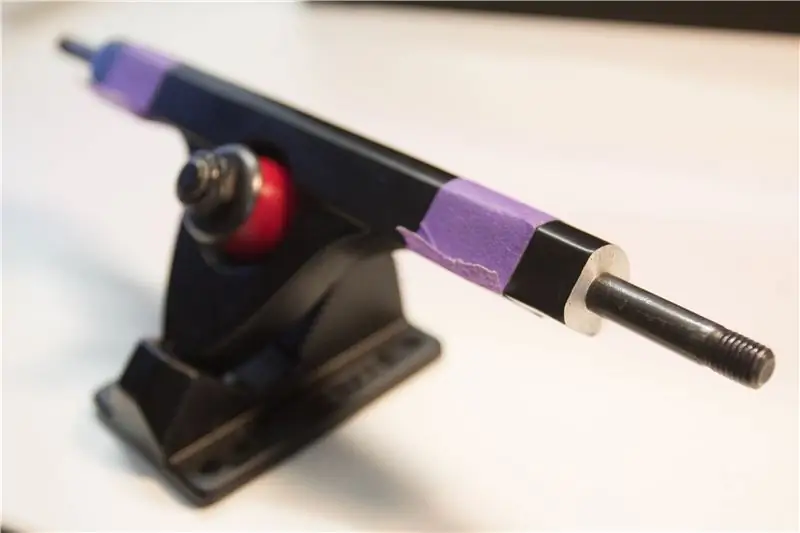
Primer vaig completar la construcció del tren motriu per assegurar un joc adequat per al recinte electrònic. He seleccionat els camions Caliber per utilitzar-los, ja que tenen un perfil quadrat que era perfecte per fixar els muntatges del motor. No obstant això, l'eix era lleugerament massa curt per permetre que els dos motors s'utilitzessin al mateix camió, de manera que vaig necessitar ampliar-lo per permetre que les rodes encaixessin.
Ho vaig aconseguir tallant una part del cos del penjador de camions d'alumini, deixant al descobert més de l'eix d'acer. Després vaig tallar la major part de l’eix cap avall, deixant uns 10 mm que podia enfilar amb un troquel M8.
Aleshores es podria cargolar un acoblament i afegir-hi un altre eix roscat, que estendria efectivament l'eix. He utilitzat el compost de retenció Loctite 648 per assegurar permanentment l’acoblador i el nou eix per assegurar-se que no es descargolaria durant l’ús. Això va permetre que els dos motors s’adaptessin al camió i va proporcionar molt de joc per a les rodes.
La transmissió es va imprimir principalment mitjançant la tecnologia HP Multi-Jet Fusion, per garantir la rigidesa i la resistència durant l’alta acceleració i frenada, on es transferirien les forces més grans.
Es va dissenyar una politja especial per bloquejar les rodes posteriors, que després es va connectar a la politja del motor amb una corretja HTD 5M. Es va afegir una coberta impresa en 3D per proporcionar protecció al conjunt de la politja.
Pas 3: Tancaments de costelles
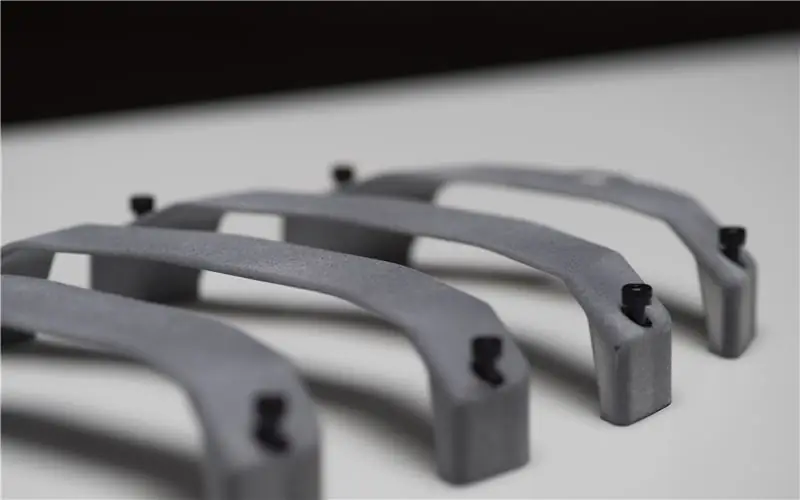
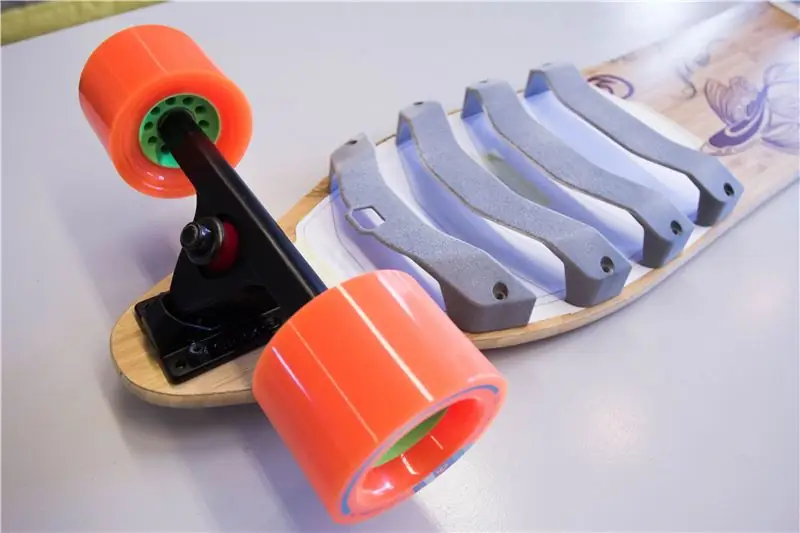
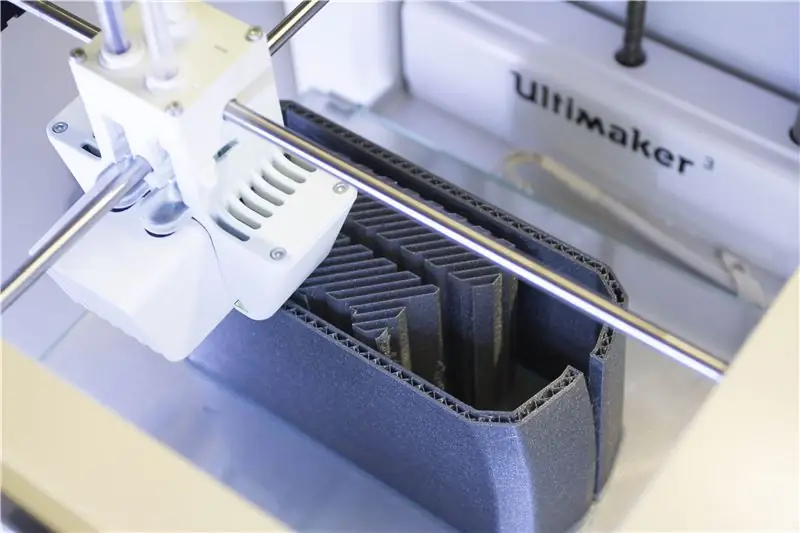
Una de les principals decisions de disseny que vaig prendre va ser separar els recintes, cosa que va donar com a resultat un aspecte net i permetre que la coberta flexible pogués funcionar sense més rigidesa dels recintes. Volia transmetre els aspectes funcionals de la tecnologia HP Multi Jet Fusion, així que vaig decidir imprimir FDM el cos principal de les carcasses que reduïa els costos, i després vaig utilitzar les peces HP per suportar-les i fixar-les a la coberta. Això proporcionava una estètica interessant i alhora molt funcional.
Els recintes impresos FDM es van dividir per la meitat per facilitar la impressió, ja que es podia eliminar el material de suport de la superfície exterior. La línia divisòria es va col·locar acuradament per assegurar-se que la part HP l’amagava quan es fixava al tauler. Es van afegir forats per a les connexions del motor i es van enganxar connectors de bala xapats en or
Les insercions roscades es van incrustar a la coberta de bambú per assegurar els tancaments al tauler i es van esmolar a ras de la superfície del tauler per garantir que no hi hagués cap espai entre la coberta i el recinte.
Pas 4: electrònica
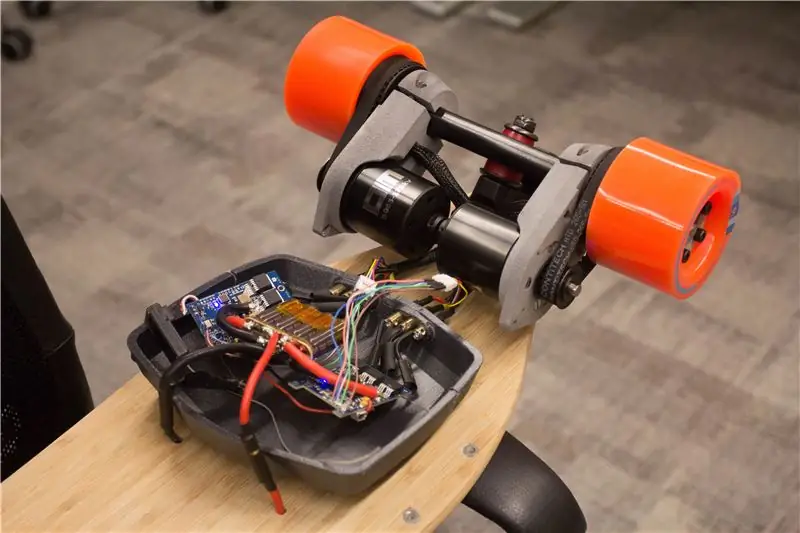
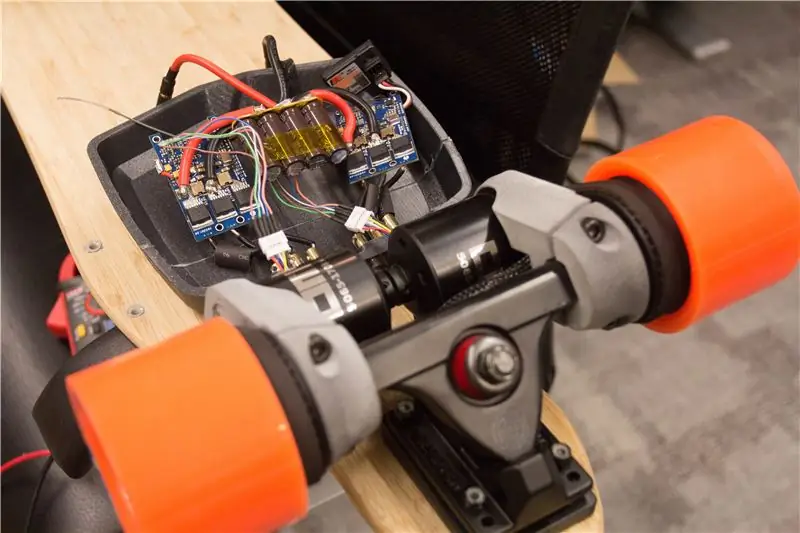
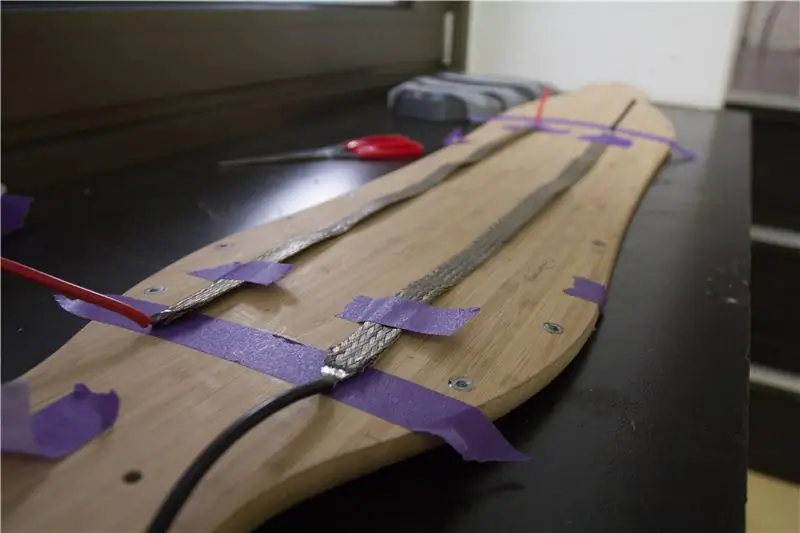
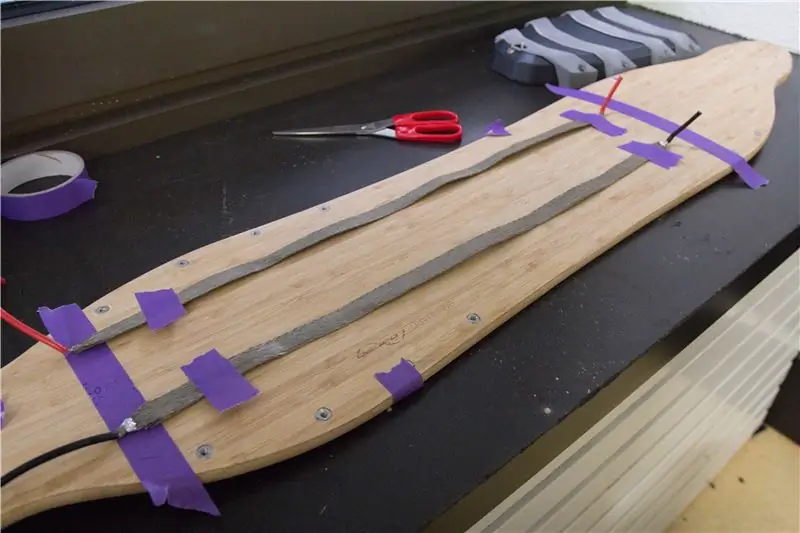
L’electrònica es va triar acuradament per garantir que la placa fos potent, però també intuïtiva d’utilitzar. Aquesta placa podria ser perillosa si es produïssin mal funcionaments, de manera que la fiabilitat és un factor molt important.
El paquet de bateries consta de 20 cèl·lules de ions de liti 18650 individuals que es solden per punts per formar un paquet de 42v. Es solden 2 cel·les en paral·lel i 10 en sèrie; les cel·les que vaig fer servir van ser Sony VTC6. Vaig utilitzar una soldadora puntual per soldar les llengüetes de níquel per formar el paquet, ja que la soldadura crea massa calor que pot danyar la cèl·lula.
L'energia del tancament de la bateria es va transferir a la caixa del controlador de velocitat mitjançant un cable trenat pla que es feia passar just a sota de la cinta adhesiva a la part superior de la coberta. Això va permetre que els cables estiguessin "amagats" i va eliminar la necessitat de fer passar cables per la part inferior que haurien semblat lletjos.
Com que es tracta d'una placa de motor dual, es necessiten dos controladors de velocitat per controlar independentment cada motor. He utilitzat el controlador de velocitat VESC per a aquesta versió, que és un controlador dissenyat específicament per a monopatins elèctrics que el fa molt fiable per a aquest ús.
Els motors utilitzats són de 170kv 5065 fora de carrera que poden produir 2200W cadascun, la qual cosa suposa molta potència per a aquesta placa. Amb la configuració actual d’engranatges, la velocitat màxima de les plaques ronda els 35 MPH i s’accelera molt ràpidament.
L'última etapa va ser crear un comandament a distància per controlar la placa. Es preferia un sistema sense fils a causa del seu funcionament més fàcil. Tanmateix, era important assegurar una alta fiabilitat de la transmissió, ja que una caiguda de la comunicació podria tenir seriosos problemes de seguretat, especialment a velocitats elevades. Després de provar uns quants protocols de transmissió de ràdio, vaig decidir que la freqüència de ràdio a 2,4 GHz seria la més fiable per a aquest projecte. Vaig utilitzar un transmissor de cotxes RC de prestatge, però vaig reduir significativament la mida transferint l'electrònica a una petita funda de mà que estava impresa en 3D.
Pas 5: Tauler finalitzat i vídeo promocional
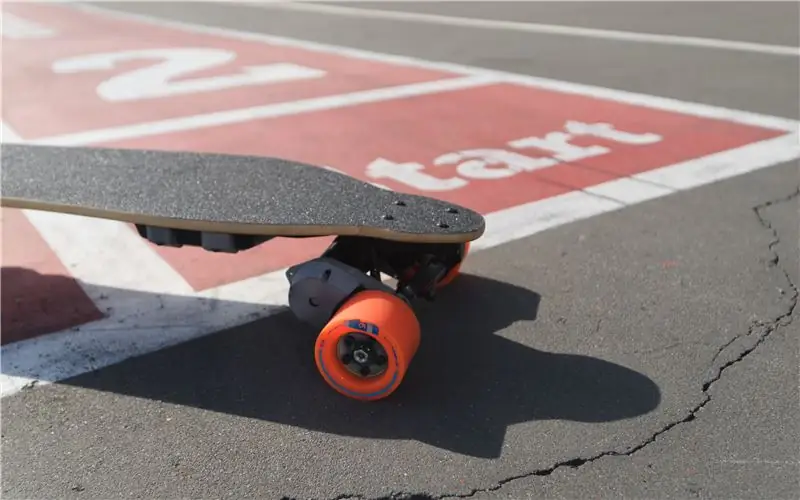
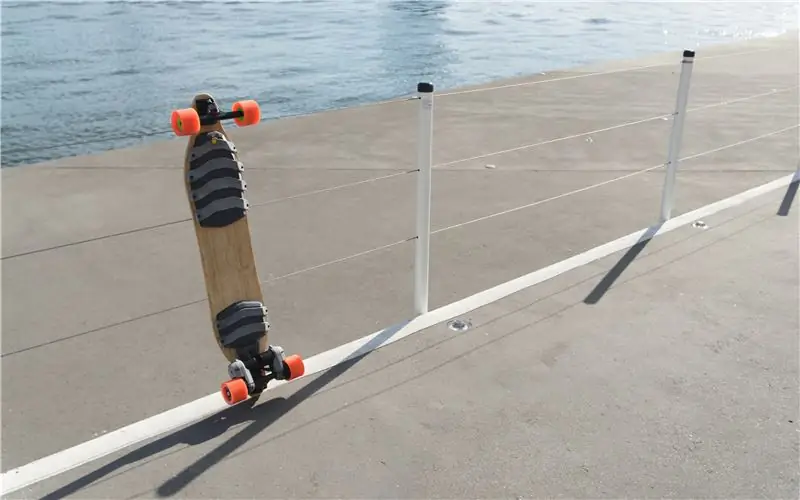
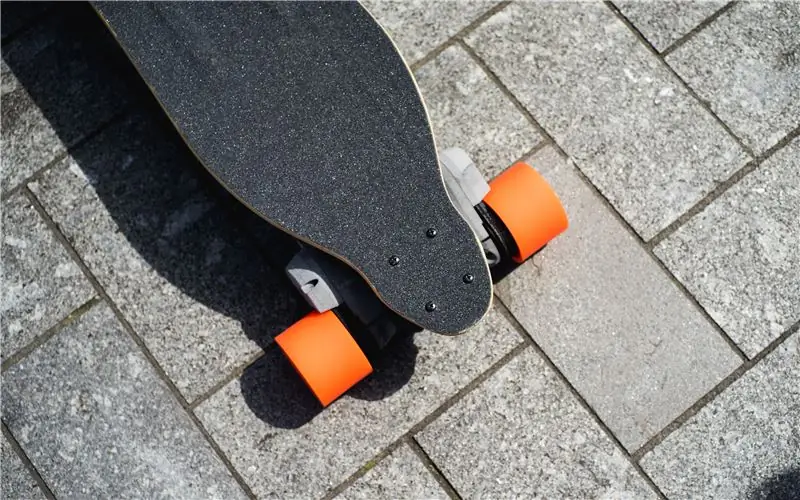
El projecte ja està acabat. Hem creat un vídeo bastant impressionant del tauler en acció, podeu veure-ho a continuació. Gràcies als concentradors 3D per permetre'm fer aquest projecte. Consulteu-los aquí per conèixer totes les vostres necessitats d'impressió 3D. 3dhubs.com
Recomanat:
Amplificador imprès en 3D d’un instrument musical elèctric: 11 passos (amb imatges)
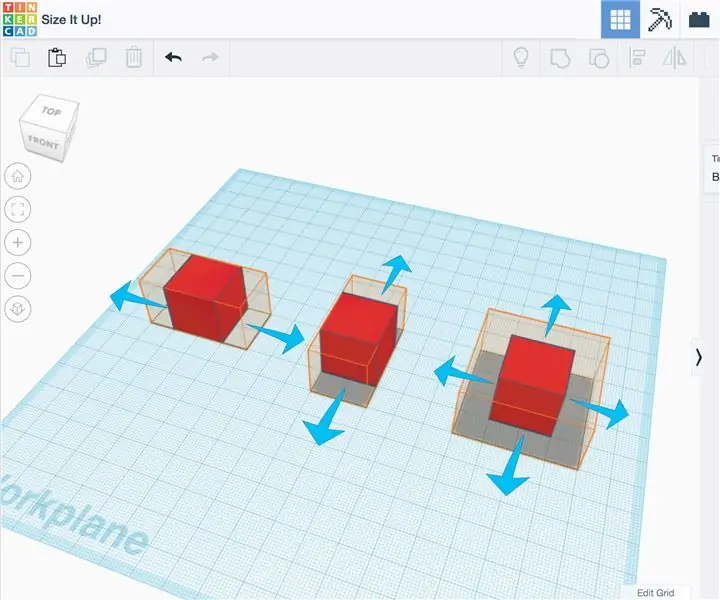
Amplificador imprès en 3D d’un instrument musical elèctric. Definició del projecte. Espero fabricar un amplificador imprimible per utilitzar-lo amb un violí elèctric o qualsevol altre instrument elèctric. Especificació. Dissenyeu tantes parts com sigui possible per imprimir en 3D amplificador actiu i mantingueu-lo petit.Ele
Interruptor de lliscament elèctric imprès en 3D (només amb un clip): 7 passos (amb imatges)
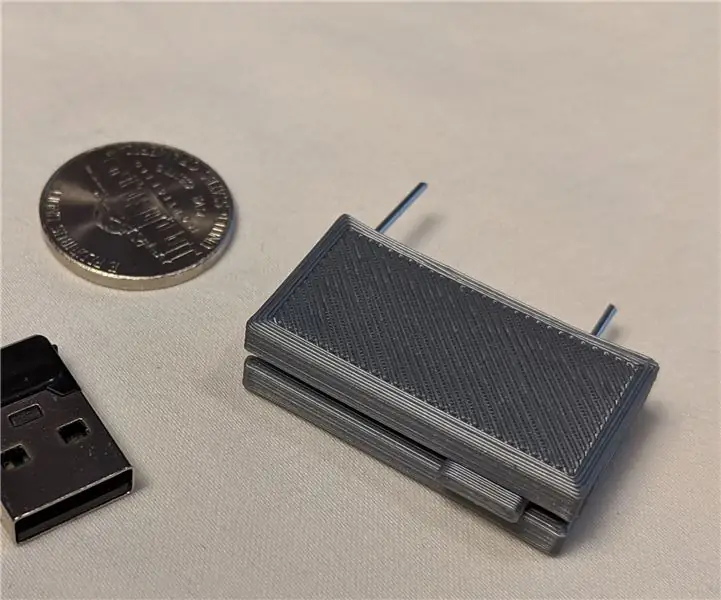
Interruptor de corredissa elèctric imprès en 3D (només amb un clip de paper): al llarg dels anys, m’he dedicat a connectar els meus petits projectes elèctrics, principalment en forma de clips de paper, paper d’alumini i cartró empedrats amb cola calenta. Fa poc vaig comprar una impressora 3D (la Creality Ender 3) i vaig anar buscant
Arbre de Nadal imprès en 3D amb LED: 10 passos (amb imatges)
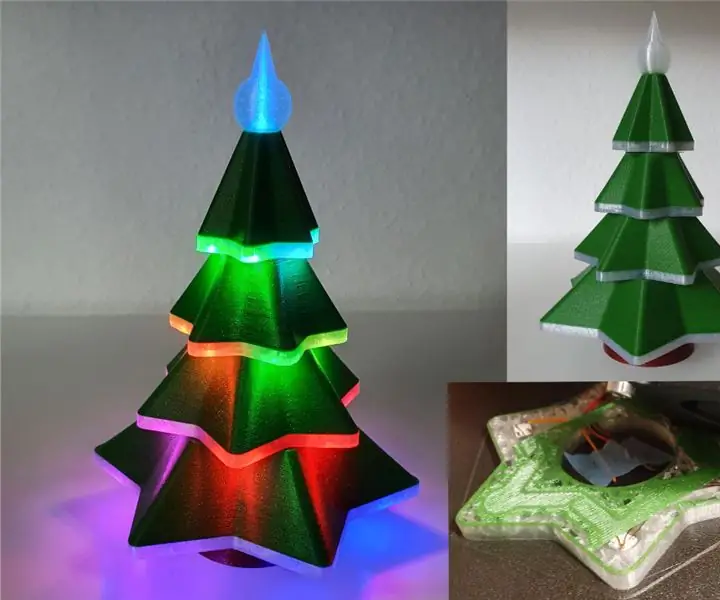
Arbre de Nadal imprès en 3D amb LED incrustat: es tracta d’un arbre de Nadal imprès en 3D amb LED adreçables incorporats al seu interior. Per tant, és possible programar els LEDs per obtenir efectes de llum agradables i utilitzar l’estructura impresa en 3D com a difusor. L'arbre està separat en 4 etapes i un element base (l'arbre
Control lliscant de càmera de seguiment d'objectes amb eix de rotació. Imprès en 3D i construït al controlador de motor CC RoboClaw i Arduino: 5 passos (amb imatges)
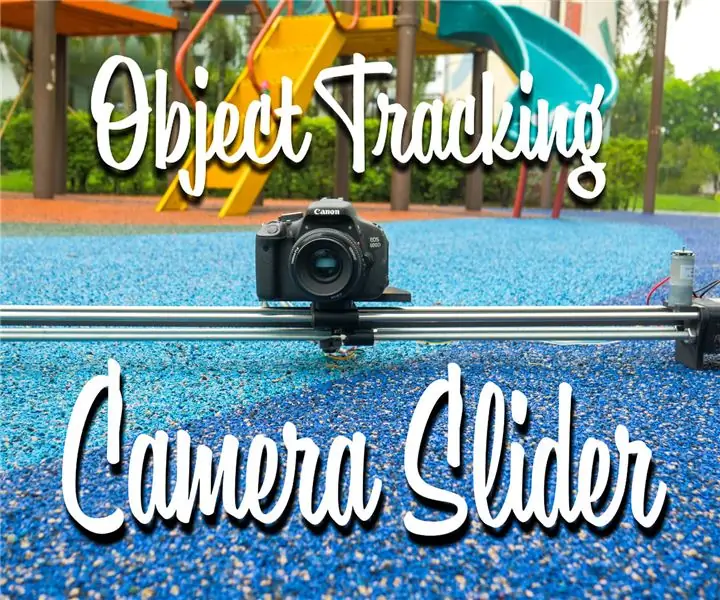
Control lliscant de càmera de seguiment d'objectes amb eix de rotació. Imprès i construït en 3D amb el controlador de motor CC RoboClaw i Arduino: aquest projecte ha estat un dels meus projectes preferits des que vaig combinar el meu interès per fer vídeo amb el bricolatge. Sempre he mirat i volgut emular aquelles preses cinematogràfiques de pel·lícules en què una càmera es mou per una pantalla mentre es desplaça per fer un seguiment
OAREE - Imprès en 3D - Robot per evitar obstacles per a l'educació en enginyeria (OAREE) amb Arduino: 5 passos (amb imatges)
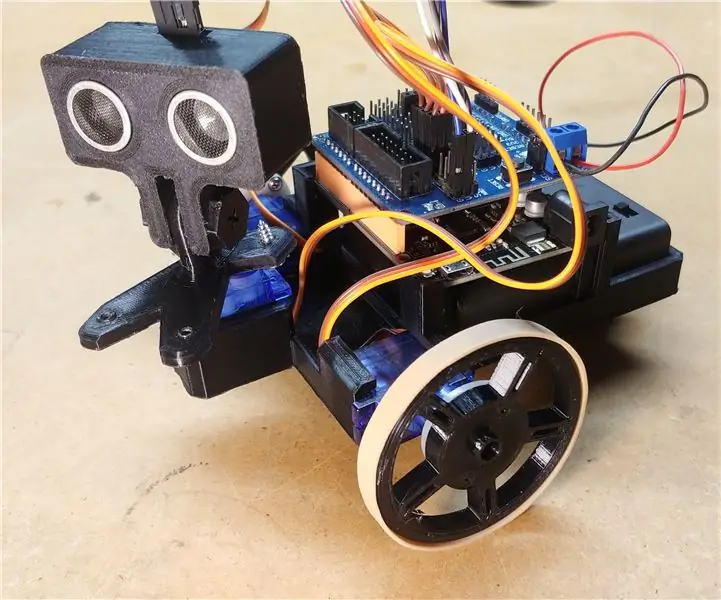
OAREE - Imprès en 3D - Robot per evitar obstacles per a educació en enginyeria (OAREE) amb Arduino: Disseny de OAREE (robot per evitar obstacles per a educació en enginyeria): l’objectiu d’aquest instructiu era dissenyar un robot OAR (robot per evitar obstacles) que fos senzill / compacte, Imprimible en 3D, fàcil de muntar, utilitza servos de rotació contínua per a movem