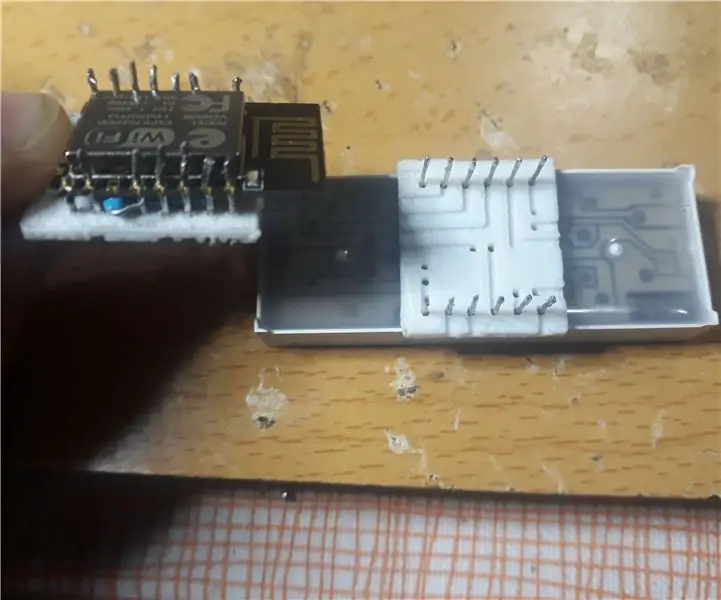
Taula de continguts:
2025 Autora: John Day | [email protected]. Última modificació: 2025-01-23 14:37
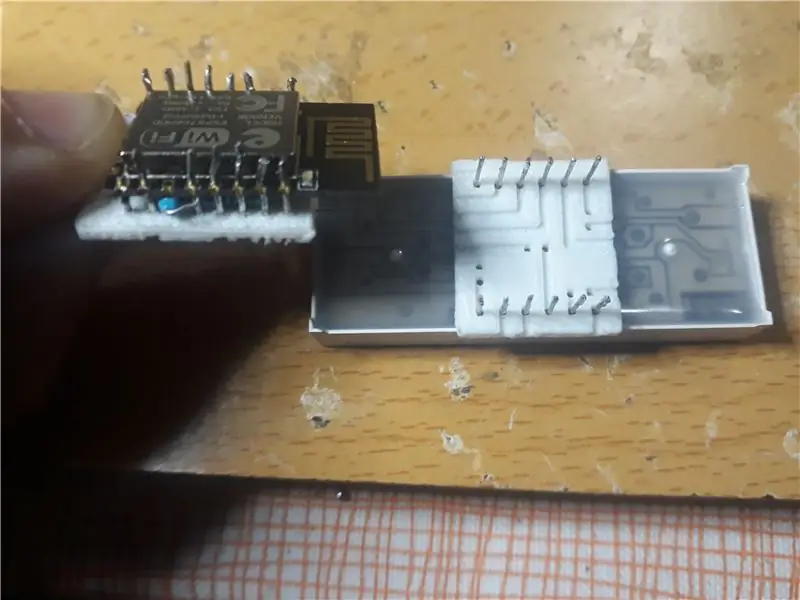
Quan vaig arribar a connectar una pantalla de 4 dígits amb 7 segments al meu Teensy, vaig decidir que havia de començar a investigar sobre la fabricació de PCB a casa d’una manera fàcil. L’aiguafort tradicional és força tediós i perillós, de manera que ho vaig descartar ràpidament. Una bona idea que he vist al voltant són els taulers impresos en 3D que funcionen afegint pintura conductiva als vostres canals, però això sembla bastant irregular per a la conductivitat. També hi ha filaments conductors especials que podeu utilitzar en una impressora de doble extrusió, però busco quelcom bàsic i eficaç per a l'equipament estàndard que tinc.
Així que he pensat a soldar i col·locar directament components i connectors en impressions 3D.
Abans de començar, tingueu en compte que imprimirem amb ABS, ja que pot resistir + 200ºC abans de deformar-se (per tant, podem aplicar-hi una mica de soldadura). Imprimir amb ABS no és tan senzill com ho és amb PLA, necessiteu una impressora inclosa i calibre molts paràmetres, però un cop ho feu bé, el resultat fa la diferència.
Per afegir un cert context, en els exemples estic creant un PCB per a la placa wifi ESP8266 12E perquè pugui connectar-lo fàcilment a qualsevol altra cosa més tard (l'objectiu final és una pantalla 4d7seg).
El PCB em permetrà utilitzar tots els pins disponibles, mentre que la majoria de mòduls tenen molt pocs pins de recanvi o tenen massa funcions addicionals que realment no vull (com el NodeMCU).
Subministraments
- Programari de disseny de PCB (KiCad aquí, gratuït). Nivell inicial.
- Programari de modelatge 3D (Blender aquí, gratuït). Nivell d'usuari.
- Una impressora 3D (Creality 3D Ender 3 Pro aquí, uns 200 €). Nivell d'usuari.
- Es recomana tenir un armari a la impressora quan utilitzeu ABS. Assegureu-vos que podeu imprimir ABS amb èxit abans de continuar amb aquesta instrucció.
- Filament ABS (Smartfil ABS, uns 20 € / Kg). 3-15 grams per PCB.
- Agulles de cosir (només n’hi ha prou de la mare). La mida dependrà del diàmetre dels pins dels components. Normalment de 0,5 mm o 1 mm de diàmetre.
- Soldador de llauna i soldador (uns 15 € d’una botiga local). A més, tots els accessoris adequats per a la soldadura: suport per a soldador, una làmpada, un tauler, pinces, ulleres de protecció, una màscara … Els accessoris corresponen a l’usuari, assegureu-vos que us sentiu còmode i segur mentre feu la mà!
- Molta paciència, una ment creativa i pròpia de la caixa i una bona base (intenteu buscar a Google i estudiar molt abans de posar-vos a les mans).
Pas 1: prototip i esquema
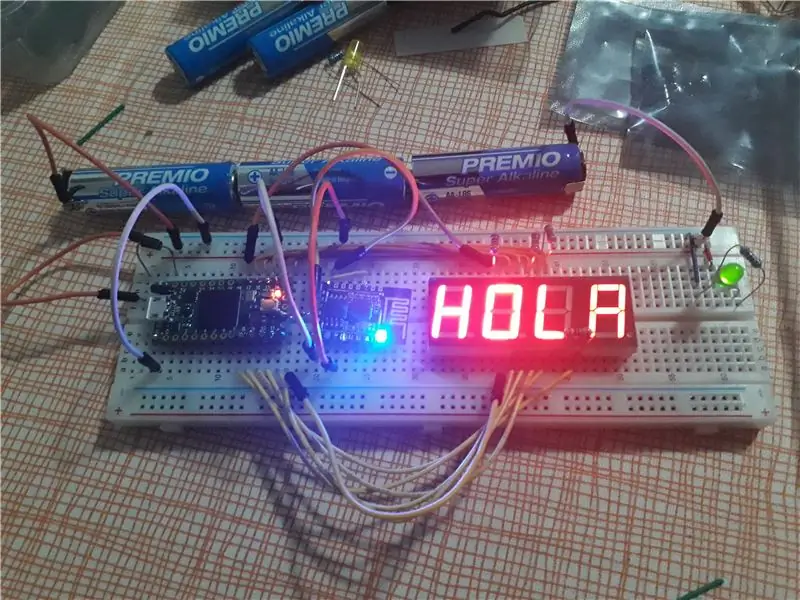
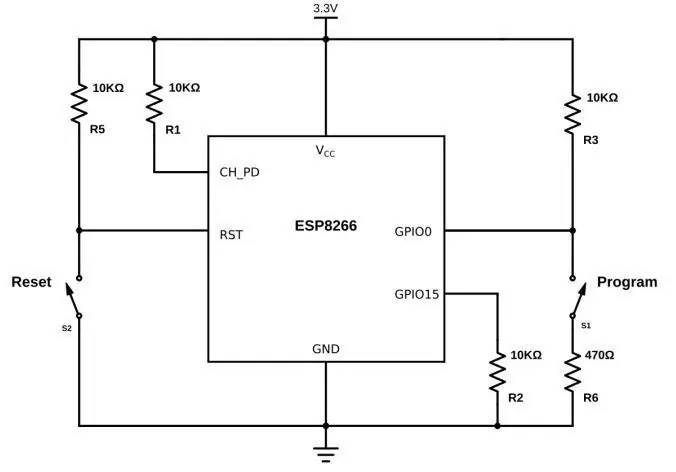
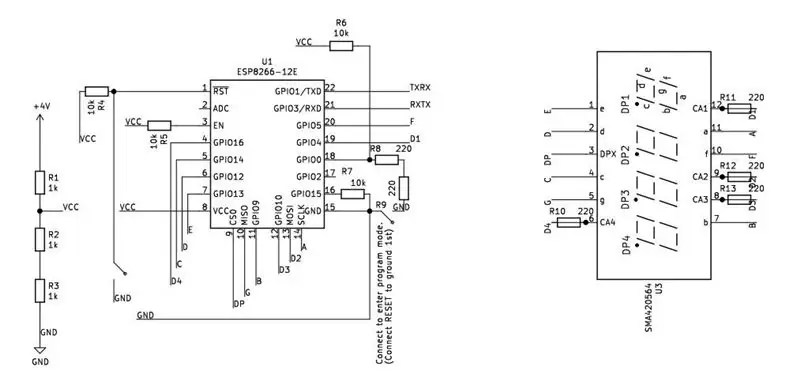
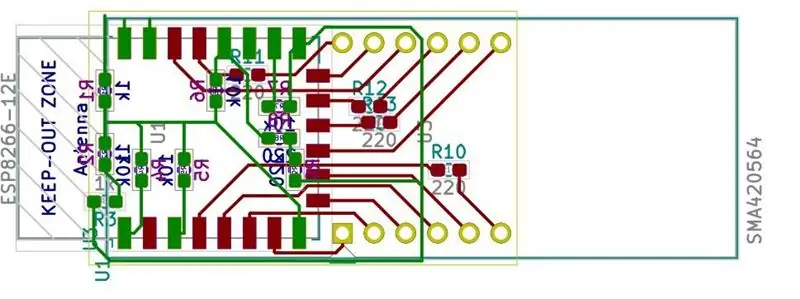
Tret que seguiu l'esquema d'una altra persona, heu de construir el circuit elèctric seguint les especificacions del fabricant. Proveu un prototip de circuit i, un cop el tingueu funcionat, dibuixeu totes les connexions i components.
Un cop tingueu un esbós i us sentiu còmode amb una comprensió clara del vostre circuit, feu-lo detallar al vostre programari EDA preferit. Això ajudarà a optimitzar i verificar el vostre disseny.
Dibuixeu el vostre esquema i utilitzeu-lo com a guia per al disseny del vostre PCB. El programari EDA com Eagle o KiCad us permetrà afegir components específics, amb pinouts i dimensions realistes, de manera que pugueu dissenyar el vostre circuit elèctric amb precisió al seu voltant.
Estic fent servir KiCad, que és lliure i prou fàcil d’entendre per començar. Tot el que sé és gràcies a Brian Benchoff @ https://hackaday.com/2016/11/17/creating-a-pcb-in… i algunes publicacions relacionades, així que seguiu les seves pautes per acabar amb un bon disseny de PCB.
Les imatges d'aquesta secció es refereixen a:
- Prototip de prova per a l'ESP8266 i una pantalla de 7 dígits de 4 dígits (connectada a un Teensy 4).
- Un esquema de cablejat de referència per a una placa wifi ESP8266 12E.
- Un esquema de KiCad per a una pantalla de 4 dígits de 7 segments que funciona a través de l’ESP8266 i un divisor de voltatge (aquest és el meu objectiu final).
- Una sortida de disseny de PCB KiCad.
Pas 2: model 3D
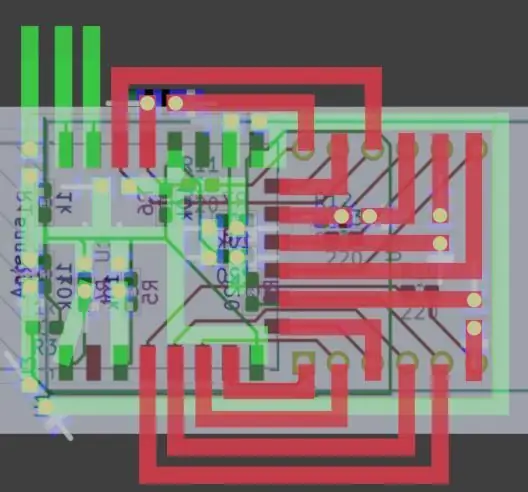

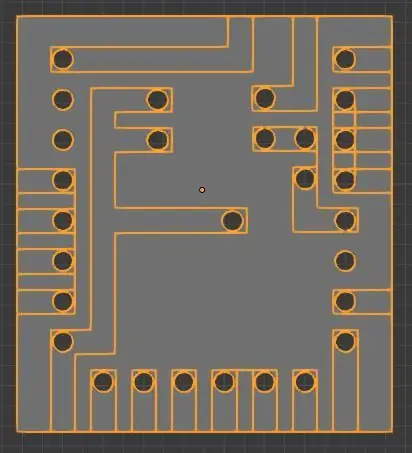
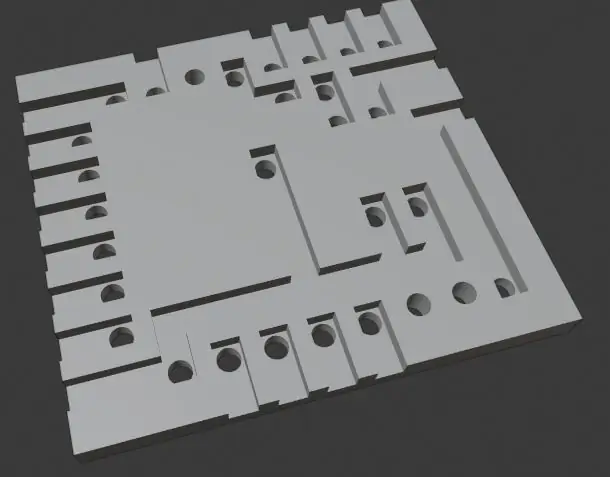
Un cop tingueu un disseny de PCB en paper, hauríeu de donar-li més realisme en un programari de modelatge 3D. Això també prepararà el fitxer per a la impressora 3D. Així ho faig a Blender:
- Creeu una malla plana i afegiu-hi la imatge de disseny de PCB. Assegureu-vos que sigui a escala i que les dimensions siguin realistes, ja que servirà com a "paper de calc".
-
Creeu components simplificats prestant especial atenció a la ubicació i mida exactes dels PINS que es connecten al vostre PCB. Obteniu les especificacions del fabricant en línia o mesureu-les vosaltres mateixos per obtenir-les prou precises. Tingueu en compte algunes atenuacions estàndard que podeu utilitzar com a referència:
- Per a taulers utilitzeu avions. Per a un PCB d'una sola cara, faig servir un gruix d'1,5 mm, per més prim que no he obtingut bons detalls en imprimir (també depèn de la configuració i les capacitats de la impressora, però ens n'anirem més endavant). Per a un PCB de doble cara he utilitzat un gruix de 2,5 mm.
- Per als pins, utilitzeu cilindres d’un diàmetre mínim d’1 mm per aconseguir que la impressora els capturi.
-
Per als canals, utilitzeu cubs d'1,2 mm d'ample. Simplement extruiràs les cares per aconseguir els teus canals.
- Localitzeu els components segons el disseny del vostre PCB. Si els components són prou realistes, podeu utilitzar-lo per comprovar si hi ha enfrontaments, però sempre permeteu espai addicional al voltant de cada element.
- Traça el circuit elèctric. Col·loqueu una malla de cubs a la ubicació del primer passador. A continuació, en mode d’edició, extrudeu les cares en línia recta seguint el disseny. Una vegada més, manteniu-ho senzill amb línies de 90º i utilitzeu tants canals com consideri. A més, permeteu una separació mínima de 0,8 mm entre parets o, en cas contrari, es perdran en imprimir. La imatge 1 següent mostra algunes rutes modificades després del modelatge amb dimensions reals, ja que la ruta ideal era massa fina per fer-la possible.
- Creeu el vostre PCB afegint un cub pla (es redueix a la mida anterior).
- Graveu els canals i els forats al tauler afegint modificadors booleans al vostre objecte PCB. Això retallarà la part del tauler que creua l'objecte objectiu del modificador booleà.
Les imatges 3 i 4 mostren el resultat final de la placa ESP8266 (model 3D a la imatge 2).
Després d'això, hauríeu de veure una impressió 3D del vostre PCB.
El darrer pas és exportar el model correctament.
- Assegureu-vos que totes les cares apuntin cap a l'exterior ("Mode d'edició - Selecciona-ho tot" Després "Malla - Normals - Recalculeu fora").
- Assegureu-vos que siguin totes cares individuals ("Mode d'edició: seleccioneu-ho tot" i, a continuació, "Edge - Edge Split").
- Exporteu com a. STL ("Només selecció" per exportar només el PCB final i "Unitats d'escena" per mantenir l'escala de les coses).
Pas 3: programari de talladora
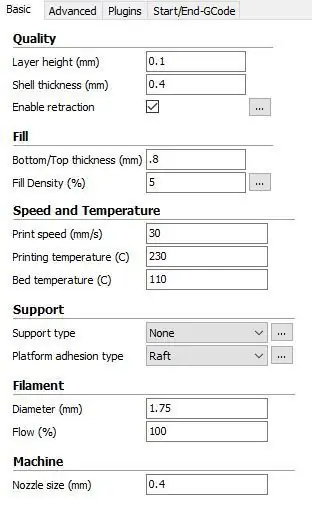
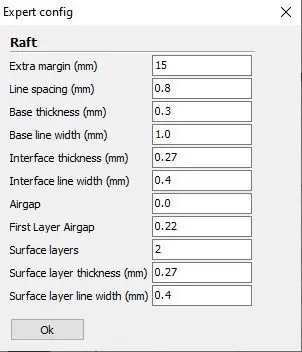
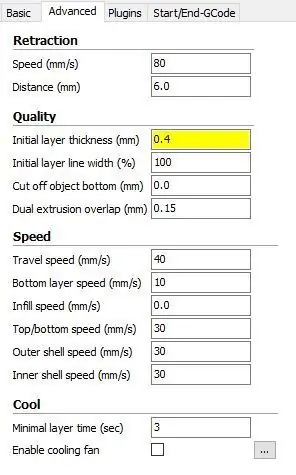
Les impressores 3D solen proporcionar un programari "Slicer" per processar els models 3D (en format.stl o altres) i calcular la ruta necessària per imprimir-lo (normalment en format.gcode). Tinc un Creality Ender 3 i no m'he mogut del Creality Slicer proporcionat, però podeu aplicar aquesta configuració a qualsevol altre programari.
Dedico una secció completa a la configuració de les talls, ja que són molt importants a l’hora d’imprimir ABS, cosa que és força complicada a causa de la deformació, la contracció i l’esquerda. La impressió d’un PCB també es troba al límit de les impressores 3D estàndard a causa de la precisió necessària.
A continuació, comparteixo la configuració que utilitzo al Creality Slicer per a la impressió detallada de PCB de l'ABS. Es diferencien de la configuració estàndard en:
- Parets i capes fines (per proporcionar prou detalls; això pot requerir un parell d'iteracions per al resultat desitjat, tret que estigueu satisfet amb la meva configuració).
- Utilitzeu una bassa. La clau està a la base, que hauríeu de tenir especial cura. (Permeto un desplaçament de 10 mm respecte al model per evitar que cap deformació mínima afecti la impressió). A més, no hi ha separacions entre línies de bassa per aconseguir una bona base sòlida. Si encerteu la vostra base, ja està tot. Si veieu que les cantonades es plegen a la base, segur que estareu condemnat.
- Velocitat lenta. Estic fent servir aproximadament 1/4 de velocitat estàndard (això permet una bona col·locació de filaments i, per tant, enganxar-se i tenir una qualitat general).
- Temperatures de l’ABS (llit: 110ºC, broquet: 230ºC)
- Ventilador desactivat (es recomana mantenir la temperatura constant per a ABS).
Pas 4: imprimeix
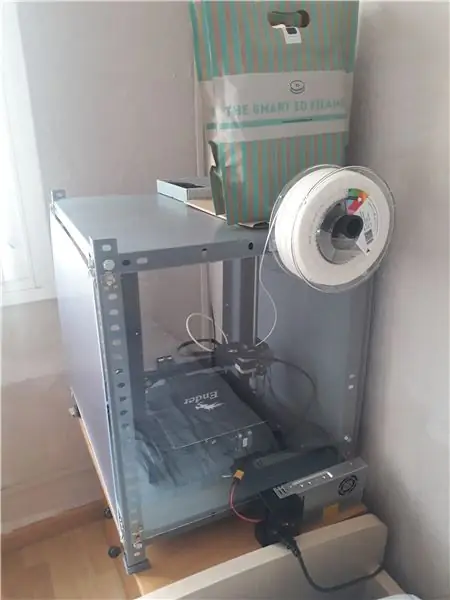
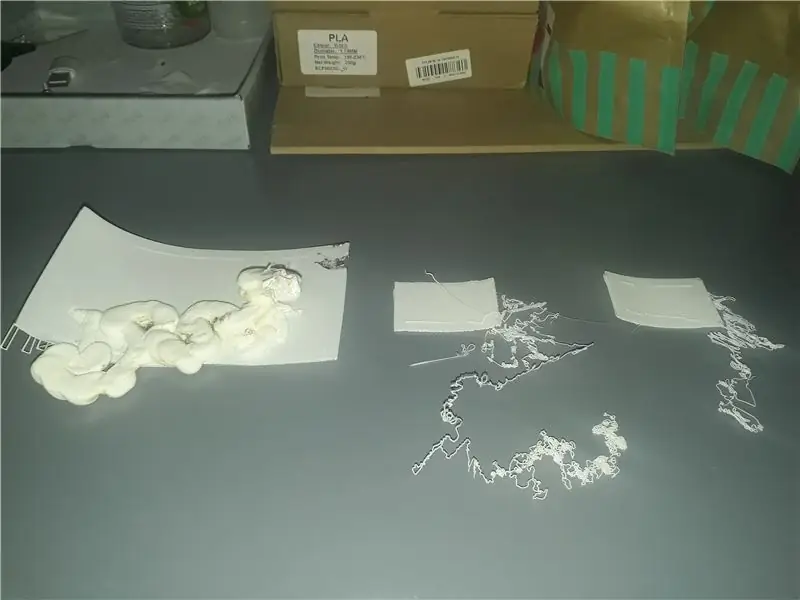
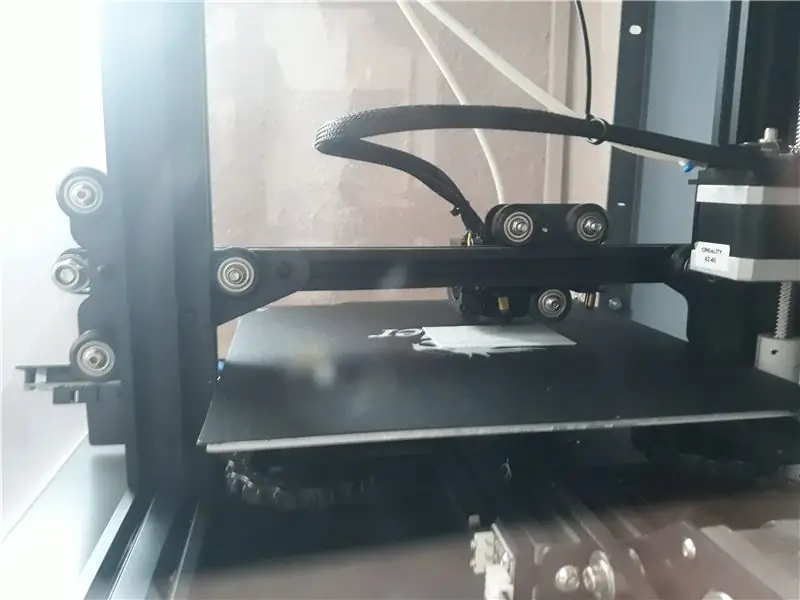
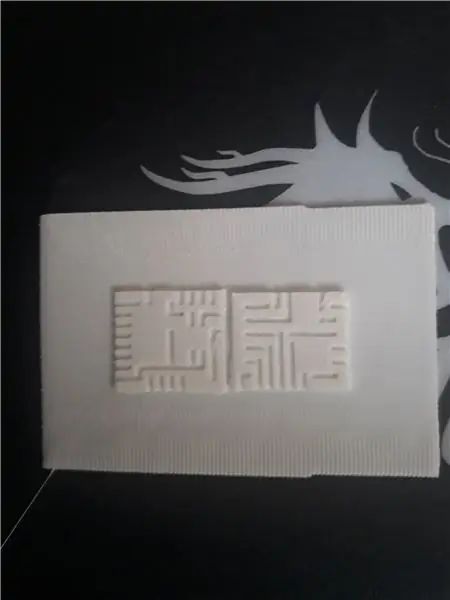
Finalment, envieu el vostre codi.g a la impressora i fabriqueu el vostre PCB. Alguns consells que heu de seguir:
- Incloeu la impressora 3D. Un recinte mantindrà la temperatura molt més estable, que és un requisit important per a la impressió ABS. Assegureu-vos de mantenir la CPU i la font d'alimentació fora del recinte, així com del filament. Si aconseguiu imprimir ABS sense cap cas, compartiu el vostre truc, ja que em torna boig.
- Escalfeu la impressora durant un temps. A PLA podeu imprimir immediatament, però amb ABS el meu consell és preescalfar amb configuracions d'ABS (llit: 110ºC, broquet: 230ºC) durant 10-15 minuts, de manera que creeu l'atmosfera adequada abans de continuar i començar la impressió.
- Imprimeix lentament però amb seguretat. Com s'ha esmentat anteriorment, he reduït la velocitat d'impressió estàndard a 1/4 al fitxer de configuració. Això demostra ser prou lent per obtenir un bon resultat, però podeu gestionar la velocitat d’impressió mentre imprimiu regulant la velocitat d’avanç si voleu optimitzar-la una mica més. Tingueu en compte que les altes velocitats provocaran moviments molt bruscs que no col·loquen el filament de manera efectiva o poden xocar amb la malla i desenganxar-lo.
- Construeix una bona base. La clau de l’ABS és aconseguir una base ben fixa. Si la base falla i es desmarca, el model ha desaparegut (vegeu alguns intents desastrosos a continuació). Amb els consells anteriors (encastament, preescalfament i velocitat lenta) hauríeu d’obtenir una bona base i un bon acabat. Però, a diferència del PLA, que deixo desatès durant hores, l'ABS necessita més atenció.
- Estigueu vigilants, sobretot al principi. Reiterant l’anterior, la clau és la base. Assegureu-vos que el primer contorn exterior estigui ben col·locat. Això conduirà la resta d’adherència de la primera capa. De vegades, el filament no s’enganxa de seguida ni s’arrossega des de la seva ubicació. Haureu de detectar-ho prou aviat per corregir qualsevol anivellament o neteja de la placa base. Vigileu sempre que no es deformin, si veieu que les cantonades augmenten, probablement acabaran descol·locant tota la base i espatllant tota la impressió. Fins i tot si la base es manté al seu lloc, la deformació farà que aquesta cantonada es deformi.
Pas 5: Cable i soldadura
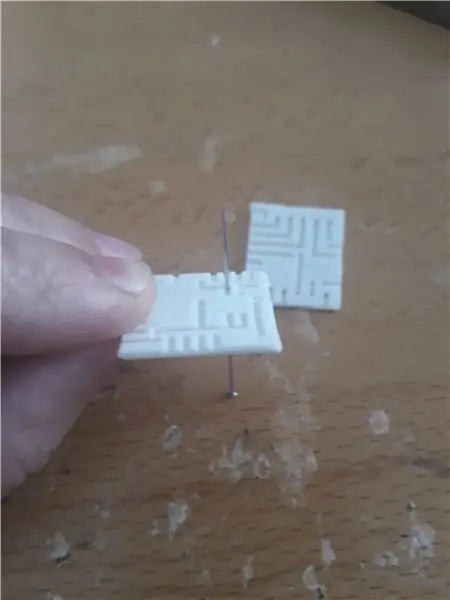
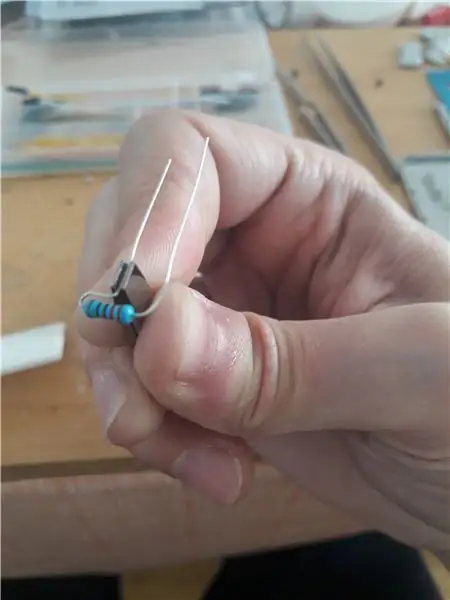
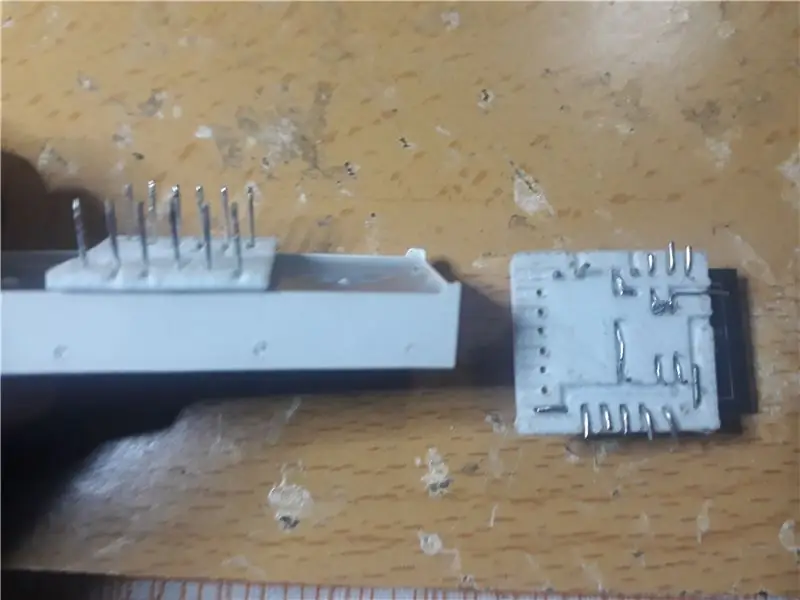
Ara és hora de posar-ho tot al seu lloc:
- Comproveu l'acabat dels canals i forats. La impressora sol faltar o sobreposar forats especialment. Utilitzeu una agulla de cosir si necessiteu tornar a obrir-ne algunes. Per descomptat, si no heu obtingut una impressió plana a causa d’una deformació o no heu obtingut el detall que esperàveu, reviseu la configuració de la impressora o, fins i tot, les dimensions del model 3D.
- Col·loqueu els components. Es poden instal·lar fàcilment mòduls, resistències, condensadors o leds que tinguin els seus propis pins. Podeu doblar lleugerament el seu propi cable per introduir-lo als canals, de manera que sigui més fàcil lligar-lo més tard.
- Afegir filferro i soldar. Utilitzeu tots els passadors o ponts que s’adaptin al canal i talleu-los de manera que només haureu de soldar en punts d’encreuament específics. No hauríem de soldar-ho tot, tot i que acostumo a fer-ho quan les coses no s’encenen. En el meu cas, vaig haver de connectar tots els passadors de l’ESP8266, i aquí va ser clau tenir bones habilitats de soldadura (que jo no). La resta de la junta era bastant senzilla de fer.
Pas 6: proveu el vostre tauler
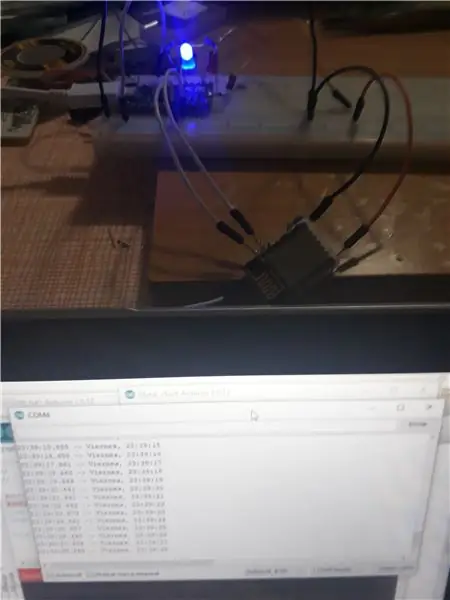
Si confieu que ho heu fet tot bé, endolleu-lo.
Per prototipar estic executant l’ESP8266 a la connexió sèrie Teensy 4.
Mentre feia les proves a la placa nua, vaig carregar un programa que carregava l’hora local a través del wifi. Com podeu veure, tot funcionava bé. Espero que també tingueu un bon resultat amb aquesta tècnica.
Recomanat:
Altaveus d'escriptori d'alta fidelitat (petits) * (impresos en 3D): 11 passos (amb imatges)
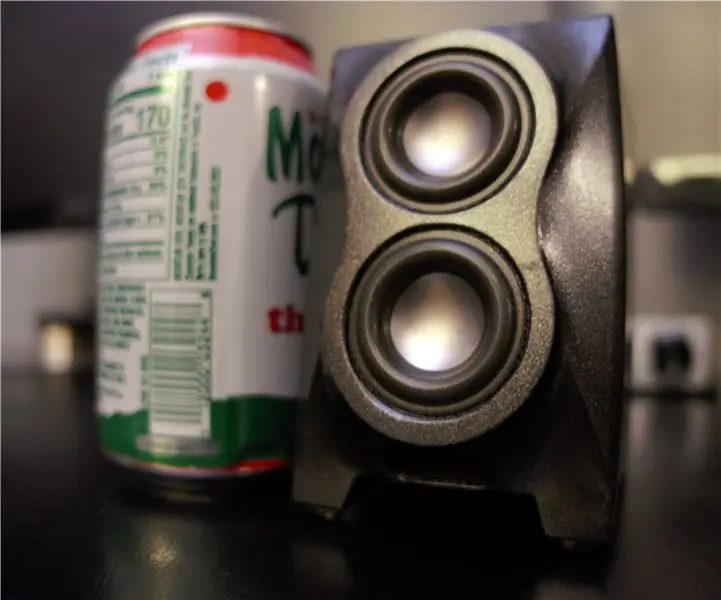
Altaveus d'escriptori d'alta fidelitat (petits) (impresos en 3D): passo molt de temps al meu escriptori. Això volia dir que passava molt de temps escoltant la meva música a través dels horribles altaveus escurats incorporats als monitors del meu ordinador. Inacceptable. Volia un so estèreo real i d'alta qualitat en un paquet atractiu
Mànecs impresos en 3D per a qualsevol objecte: 10 passos (amb imatges)
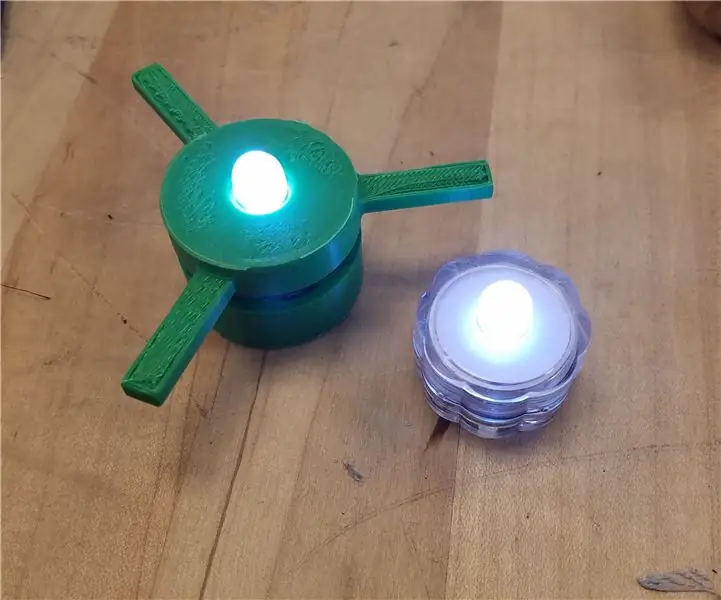
Mànecs impresos en 3D per a qualsevol objecte: si sou com jo, us agrada fer coses, però teniu problemes a l’hora de tractar projectes que requereixen un alt nivell de destresa. De vegades, sobretot si he estat fent feines a petita escala, tinc problemes per continuar treballant
Auriculars Bluetooth DIY (xip BK8000L) impresos en 3D: 6 passos (amb imatges)
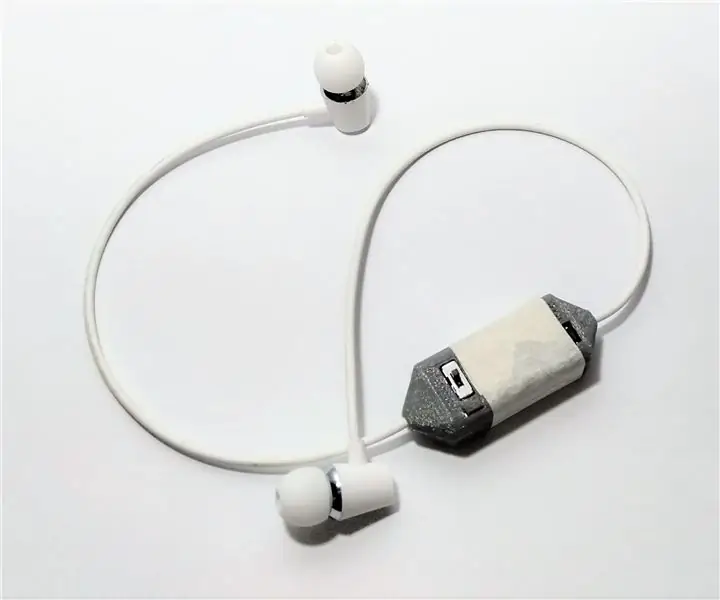
Auriculars Bluetooth de bricolatge (xip BK8000L) impresos en 3D: Hola, aquí voldria mostrar-vos com fabricar els vostres propis auriculars bluetooth sense fils. La meva motivació per fer aquest projecte és el fet que hi ha molts auriculars bluetooth dolents que he comprat recentment, així que fent el meu propi puc modificar i desenvolupar
Littlebots: robots Arduino Android impresos en 3D simples: 13 passos (amb imatges)
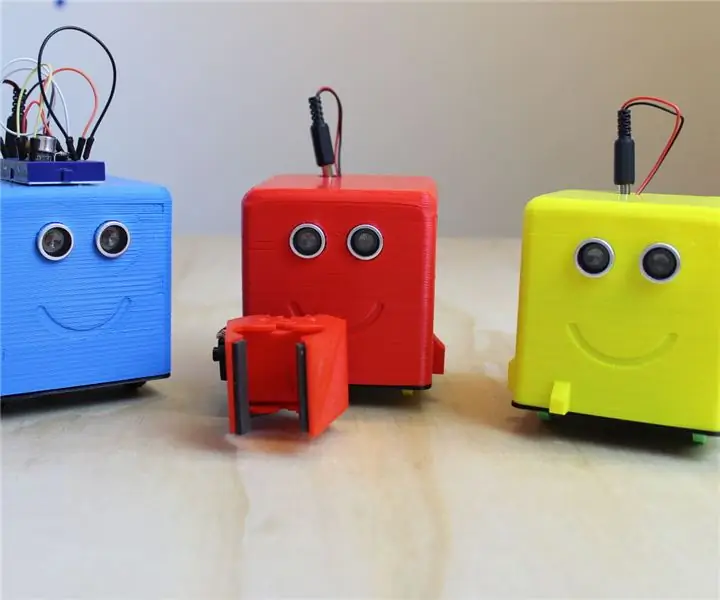
Littlebots: robots Arduino Android impresos en 3D simples: LittleBots van ser creats per ser una simple introducció a la robòtica. Mostra tots els components necessaris de la robòtica, la detecció, la presa de decisions i l’articulació, tot en un paquet agradable i senzill de muntar. El LittleBot està totalment imprès en 3D, cosa que permet
Creació de plaques de circuits impresos amb una impressora INKJET: 8 passos (amb imatges)
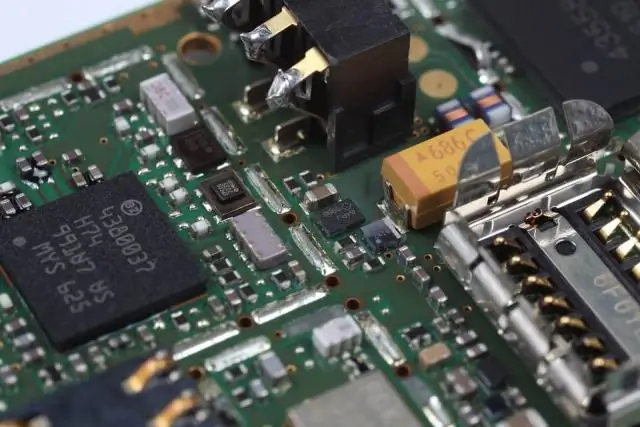
Creació de plaques de circuits impresos amb una impressora INKJET: Quan vaig començar a estudiar com gravar les meves pròpies plaques de circuits impresos, cada instructiu i tutorial que trobava feia servir una impressora làser i es planxava sobre el patró d'alguna manera. No tinc cap impressora làser, però tinc una tinta econòmica